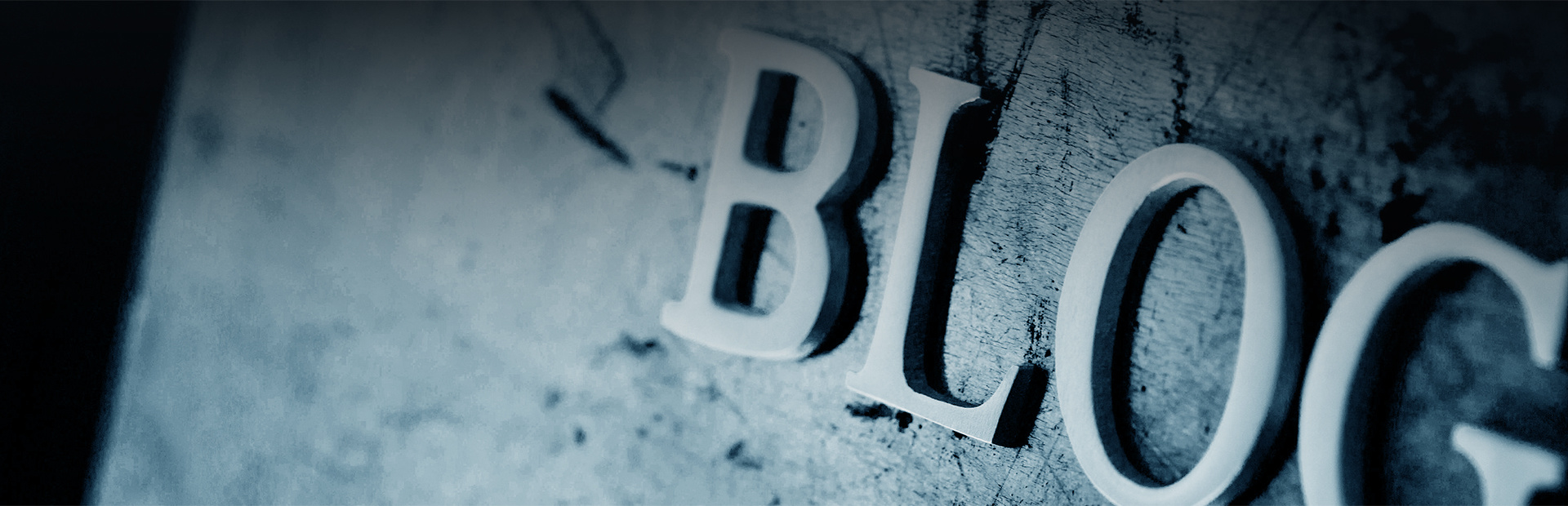
29
2023
-
05
SURFACE TREATMENT
Author:
The surface treatment of lamp products mainly includes polishing, spraying and electroplating 1. Polishing: it is a process method to reshape the surface of the workpiece with electric grinding wheel, hemp wheel and cloth wheel. The surface of the main needle die casting, stamping parts and spinning parts is generally used as the front process of electroplating. Can also be used as Surface effect treatment of materials (such as sunflower).
The surface treatment of lamp products mainly includes polishing, spraying and electroplating
1. Polishing: it is a process method to reshape the surface of the workpiece with electric grinding wheel, hemp wheel and cloth wheel.
The surface of the main needle die casting, stamping parts and spinning parts is generally used as the front process of electroplating. Can also be used as
Surface effect treatment of materials (such as sunflower).
2. Spraying:
① Principle / advantages:
When working, the spray gun, spray plate and spray cup of electrostatic spraying are connected to the negative electrode, and the workpiece is connected to the positive electrode and grounded. Under high voltage
Under the action of the high voltage of the electrostatic generator, a static state is formed between the end of the spray gun (or spray plate, spray cup) and the workpiece
Electric field. When the voltage is high enough, an air ionization zone is formed near the end of the spray gun. Resins and pigments in coatings
Most of them are composed of high molecular organic compounds, and most of them become conductive dielectrics. The coating is sprayed after being atomized by the nozzle,
The atomized coating particles are charged by contact when they pass through the pole needle of the muzzle or the edge of the spray plate and the spray cup. These are negatively charged
The charged coating particles move toward the surface of the workpiece with positive polarity under the action of the electrostatic field and are deposited on the surface of the workpiece to form
2. Spraying:
① Principle / advantages:
When working, the spray gun, spray plate and spray cup of electrostatic spraying are connected to the negative electrode, and the workpiece is connected to the positive electrode and grounded. Under high voltage
Under the action of the high voltage of the electrostatic generator, a static state is formed between the end of the spray gun (or spray plate, spray cup) and the workpiece
Electric field. When the voltage is high enough, an air ionization zone is formed near the end of the spray gun. Resins and pigments in coatings
Most of them are composed of high molecular organic compounds, and most of them become conductive dielectrics. The coating is sprayed after being atomized by the nozzle,
The atomized coating particles are charged by contact when they pass through the pole needle of the muzzle or the edge of the spray plate and the spray cup. These are negatively charged
The charged coating particles move toward the surface of the workpiece with positive polarity under the action of the electrostatic field and are deposited on the surface of the workpiece to form
Previous page